In my workshop for years there was a novel three legged stool that I’d picked up at the dump. I call it novel because the leg braces were quite clever. Where they adhered to the legs they had a vertical orientation and where they joined to each other they had a horizontal orientation. I’d tried to fashion similar braces as some sort of homage, with the intent of making a copy, but that was a little above my skill level back then, maybe still is.
I used it one day to stand on while trying to get a rope saw thrown over some high branch. This was beyond the service capacity. Result below.
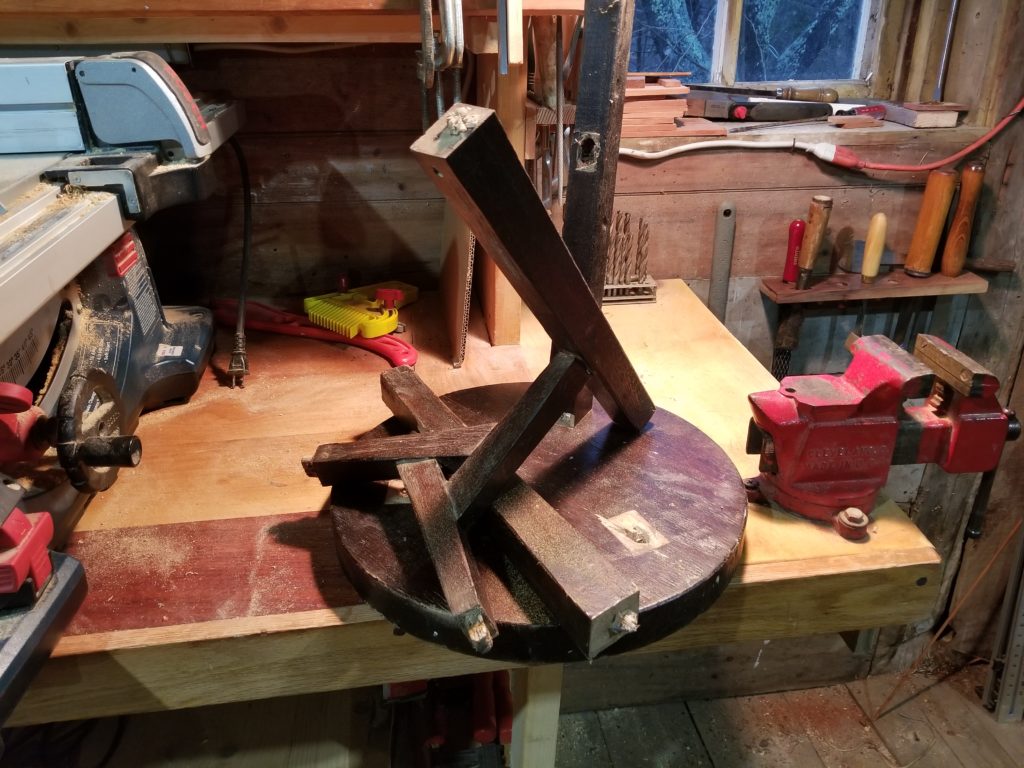
The pieces were saved, probably fallow for four years.
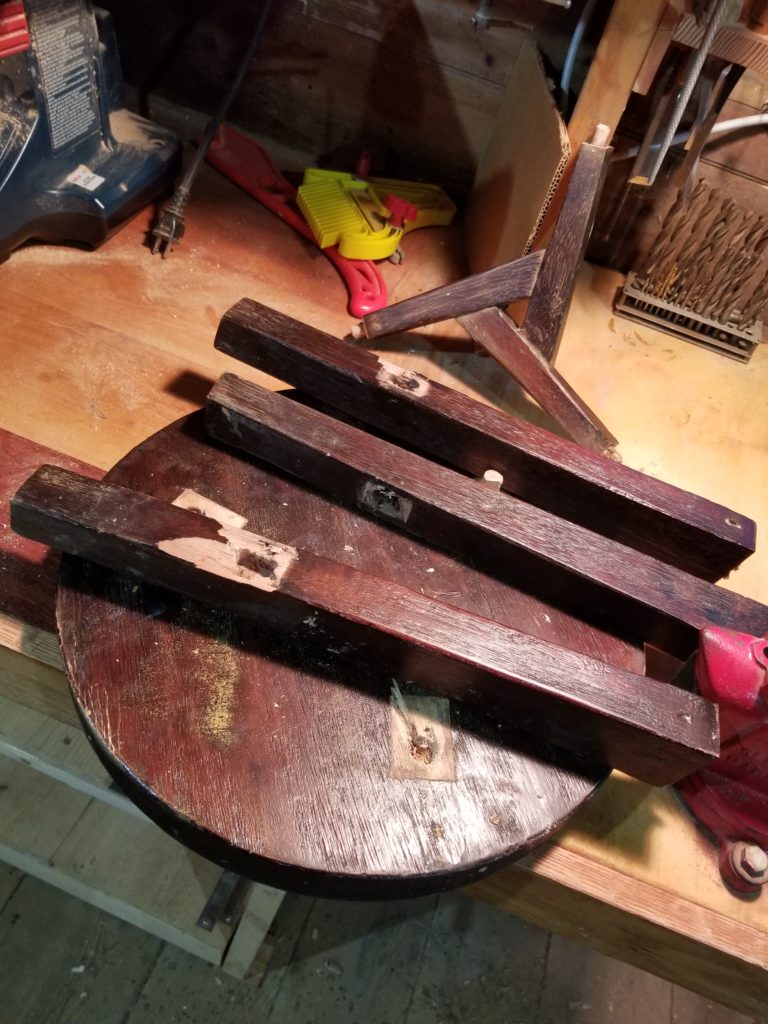
Repair me
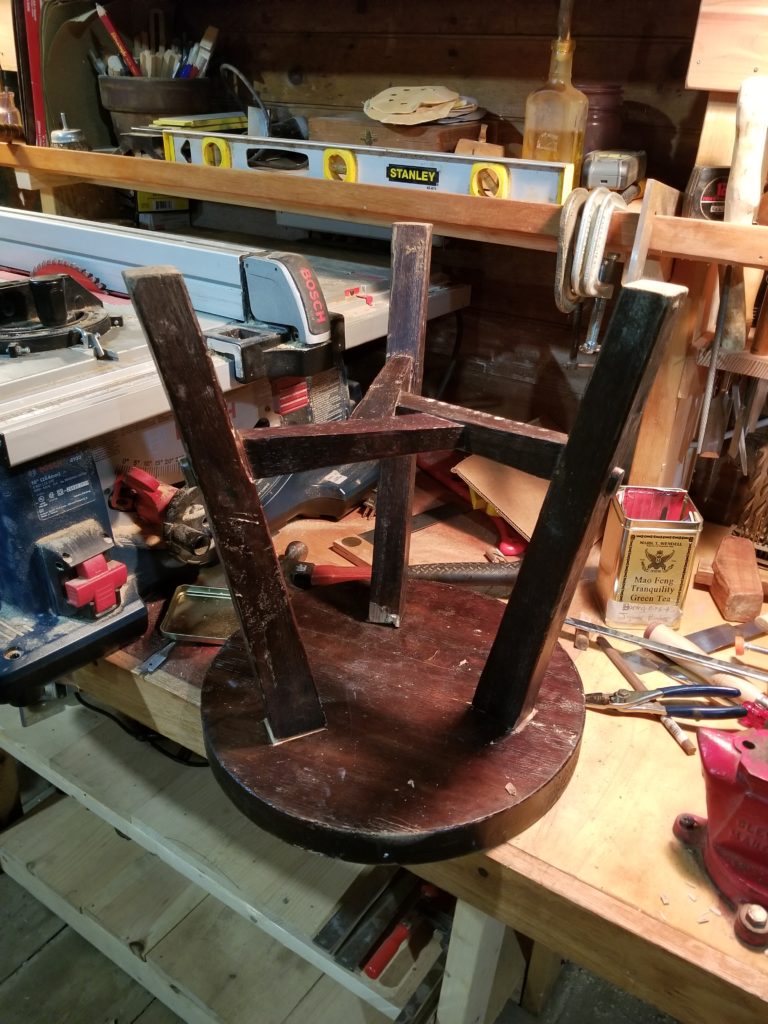
While normally I never use metal in woodwork, here I sank screws through the legs into the braces.
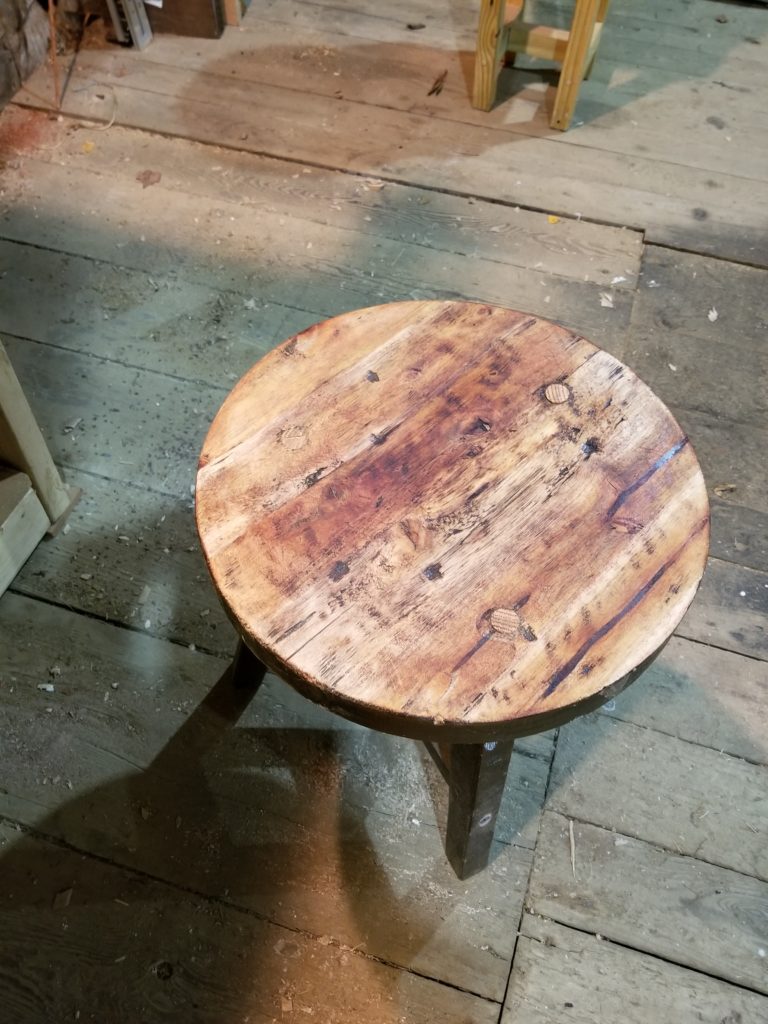
The dowels that had connected legs to seat were half inch. I replaced with 5/8 oak, hoping to gain a little strength.
All in all a most satisfactory exercise, a clearly useful outcome. So useful in fact, that I must add this little post-script.
We know that it is stated that virtue is its own reward. As a reward for this virtuous repair I got to use the stool. One thing I used it for was to hold up a 20 foot oak 6×6 that I was cutting at the twelve foot mark. When the eight foot piece came off the weight on the remaining 12 shifted in such a manner that the little milking stool was again sorely taxed. The leg assembly testified beautifully, as did its adherence to seat. It was the seat itself that broke in half.
I quickly harvested this opportunity to repair the seat. All is well in this corner of Mudsville,